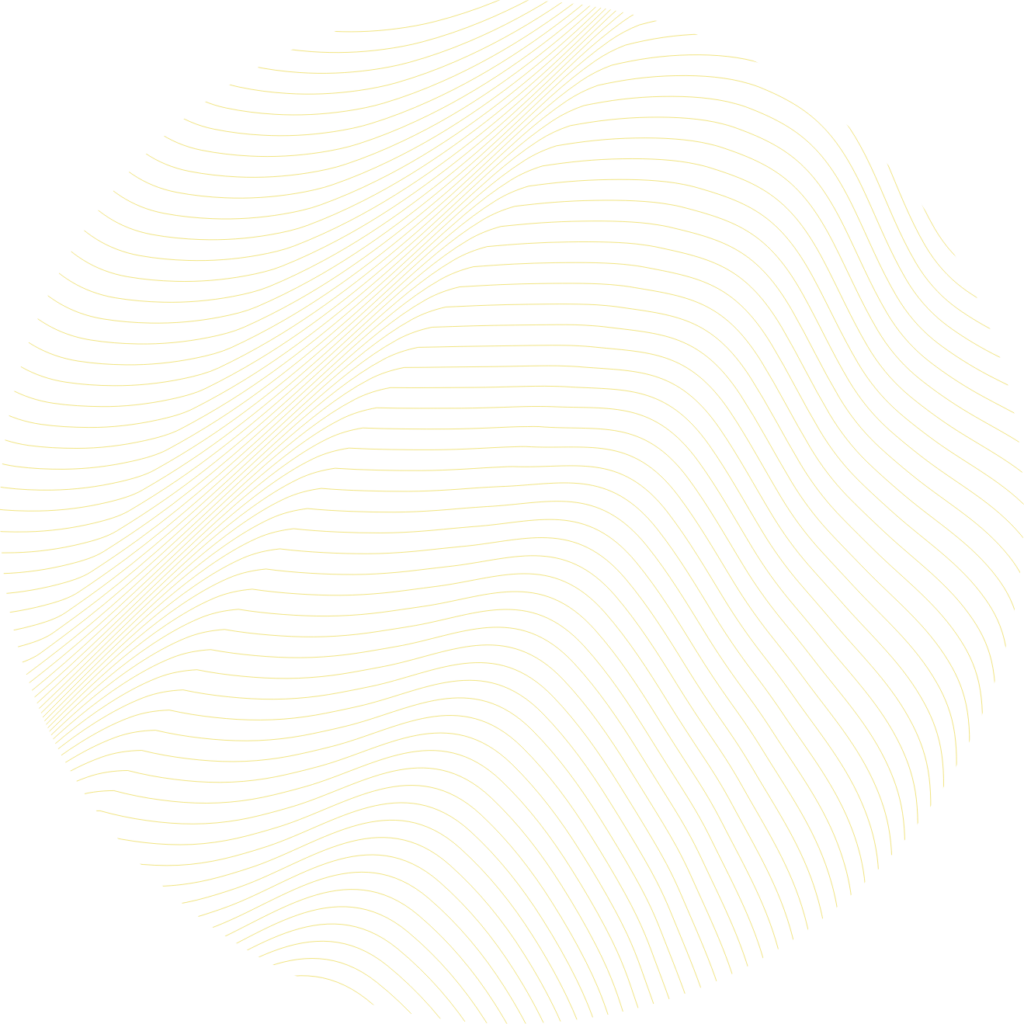
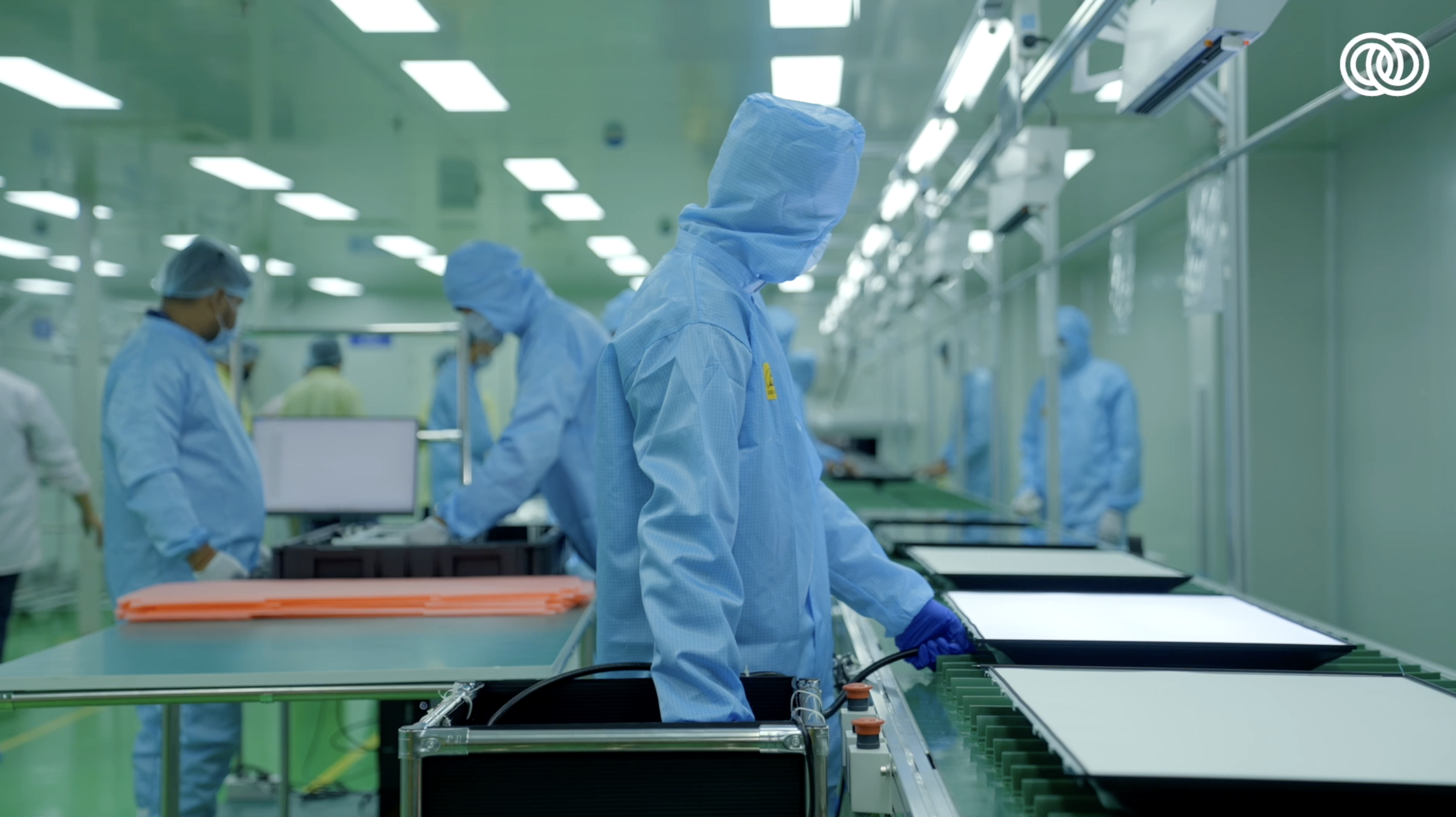
- Located on the Delhi – Mumbai corridor (NH-8, Dharuhera, Haryana), the factory is 50 km from the nearest international airport and is well connected through roads and railways. It is one of the most extensive TV manufacturing facilities in North India, spread across more than 1.20 lakh sq. ft
- This state of art facility is a one-stop solution for consumer electronics manufacturing, that provides customized solutions, better pricing, advanced R&D, shorter lead times and a strong grasp on entire supply chain management while inculcating a team of members that holds in depth and decades of experiences across this domain.
- We are the proud leading player in the digital manufacturing space developed through its partnership with leading global suppliers & in-house manufacturing capabilities.
- Factory facility is well equipped with all basic and complex level QMS to support the fast pace environment and infrastructure.
- With its two best-in-class, fully automatic, high-speed assembly lines spanning 186 meters with in-line aging capabilities. The facility is spread over 12,000 sq.m. with an installed capacity of two million 24 to 120-inch TV units annually.
- Our capabilities stands out in providing : In-house feasibility for compatibility of Motherboards with BLU, in-house OS-UI fulfillment, developing new processes to reduce weight and increase strength, Functional enhancement capabilities, AQ/PQ customisation as per customer requirement and developing new features, compliance & safety standards backed by SEDEX/SMETA & ISOs and many more.
Quality Management System
At ZPIXEL, we prioritise quality control to ensure our products meet high safety, reliability, and performance standards.
Incoming Quality Control:
Incoming Quality Control encompasses the essential task of inspecting and testing the components received from suppliers. Through careful examination, we verify that these components meet the required size, specifications, and aesthetic considerations.
In-Process Quality Control:
In-Process Quality Control plays a vital role in our manufacturing process. It involves ongoing monitoring and testing of the devices as they are assembled. As a result, each manufacturing process step is executed accurately and according to the established standards.
Functional Testing:
Functional Testing is a crucial phase where we evaluate the device’s various functions to ensure optimal performance. For example, we conduct thorough tests on the screen, battery life, processing speed, and connectivity features to guarantee their proper functionality.
Environmental Testing:
Environmental Testing subjects the device to various ecological conditions, including extreme temperatures, humidity, and vibration. Doing so ensures that our devices can endure regular use and potential mishandling, thus maintaining reliability.
Durability Testing:
Durability Testing assesses the device’s resistance to damage, such as drops and scratches commonly occurring during everyday use. Comprehensive testing ensures our devices withstand normal wear and tear, providing long-lasting durability.
Safety Testing:
Safety Testing evaluates the device’s safety features, such as electrical safety and radiation emission. This step guarantees that our products adhere to rigorous safety standards, ensuring they are safe for use by our customers.
Final Quality Control:
Final Quality Control marks the last stage before packaging, where a meticulous inspection occurs. We ensure the device meets all the required specifications and standards. In addition, any defects or issues are addressed, guaranteeing that only high-quality devices are shipped to our valued customers.
ERP:
ERP (Enterprise Resource Planning) is a powerful tool that enables unparalleled visibility, coordination, and management across various business processes. By utilising ERP, we enhance operational efficiency, allowing for effective integration and streamlined workflows throughout our organisation.
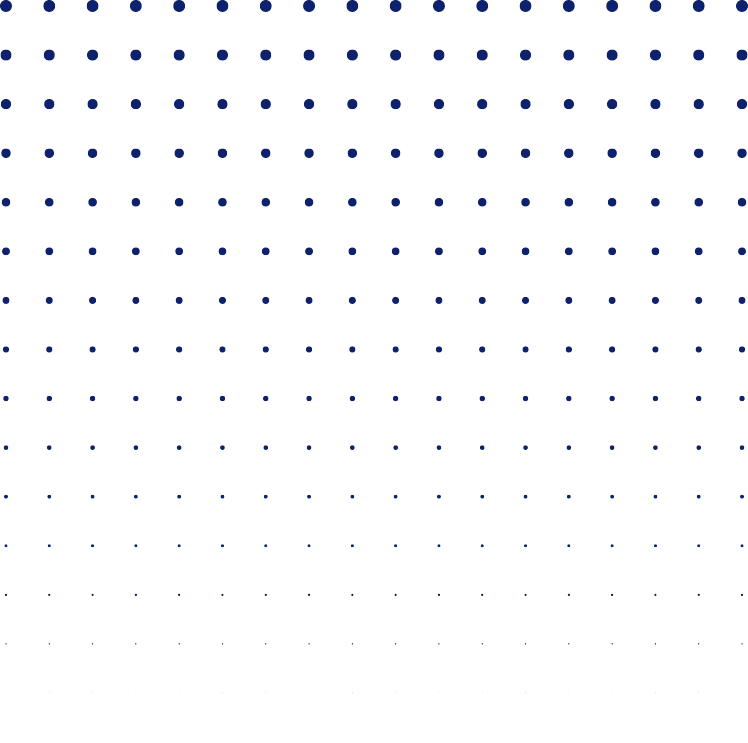
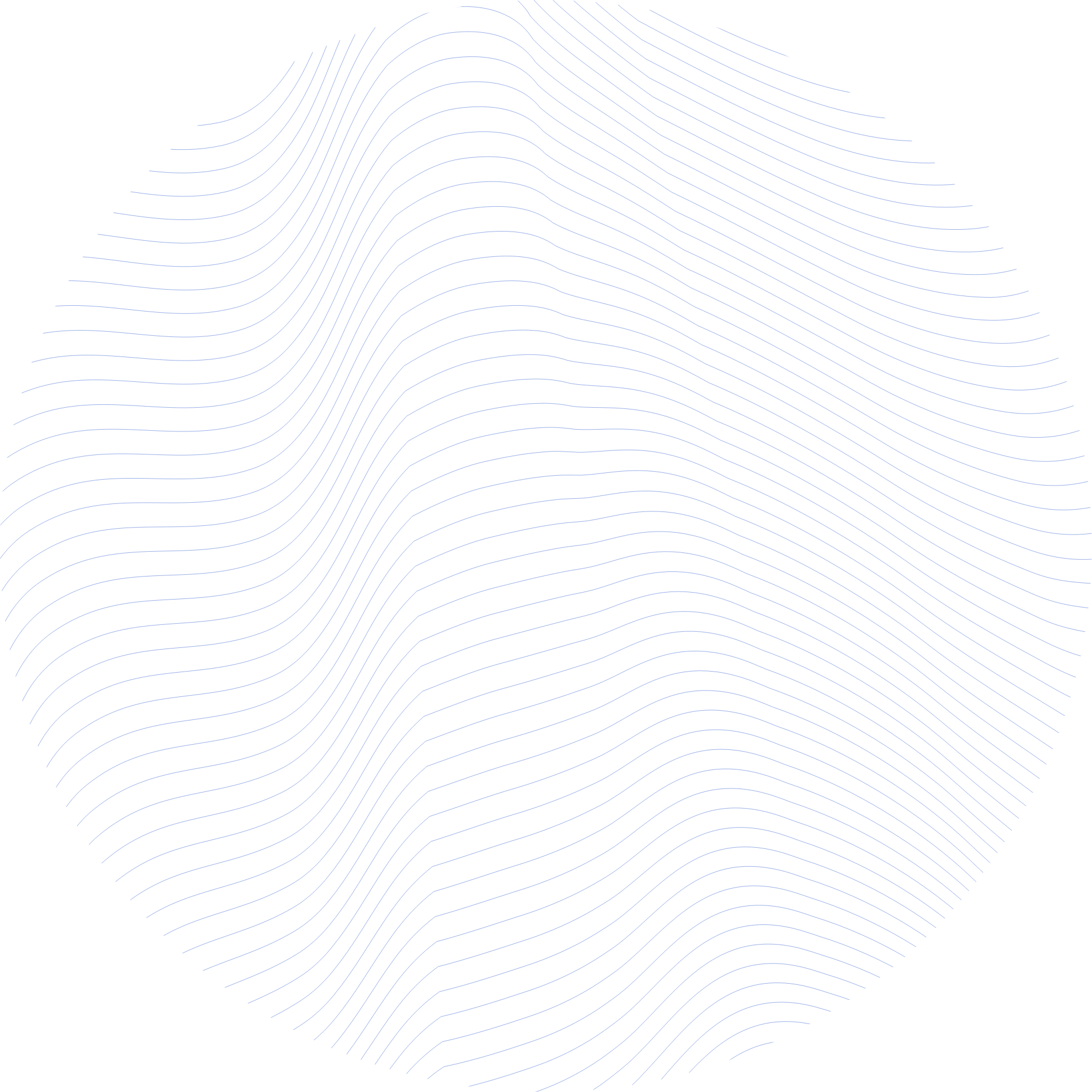
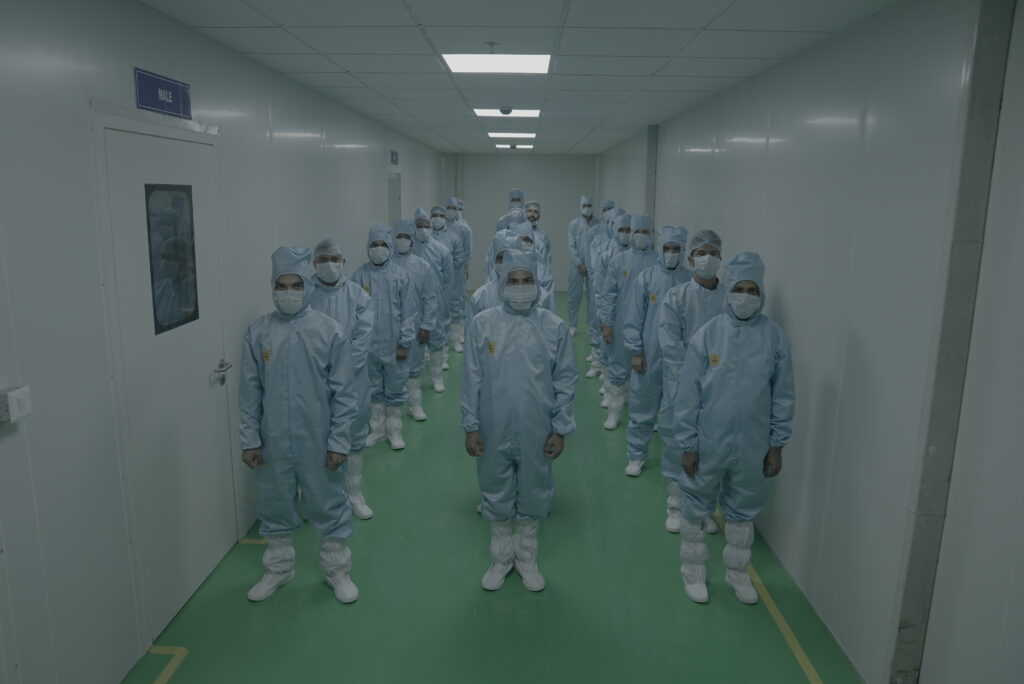
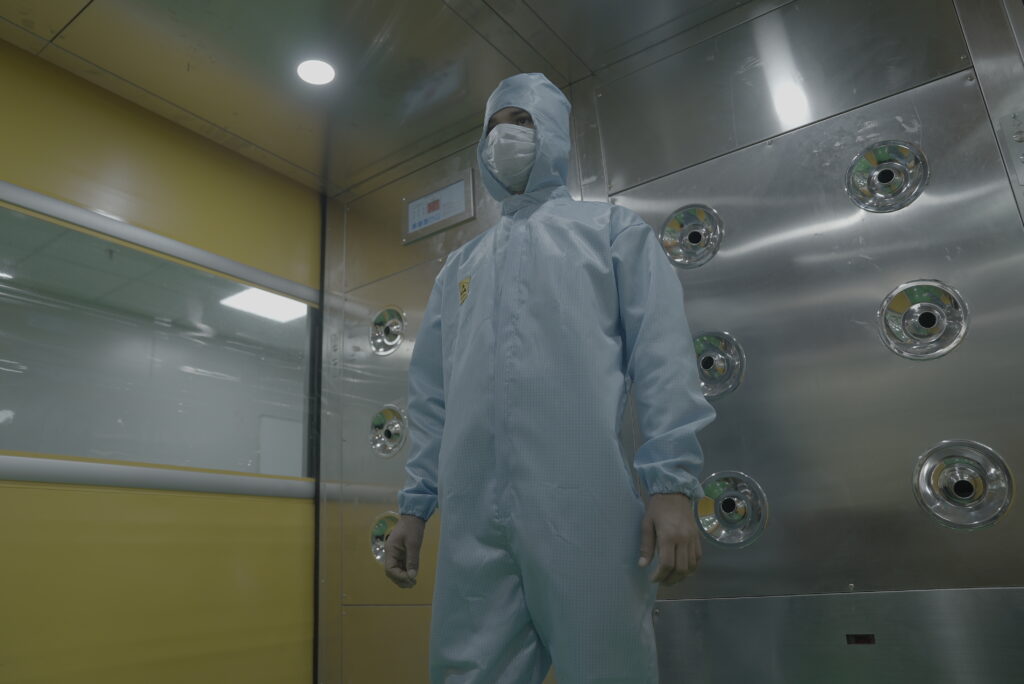
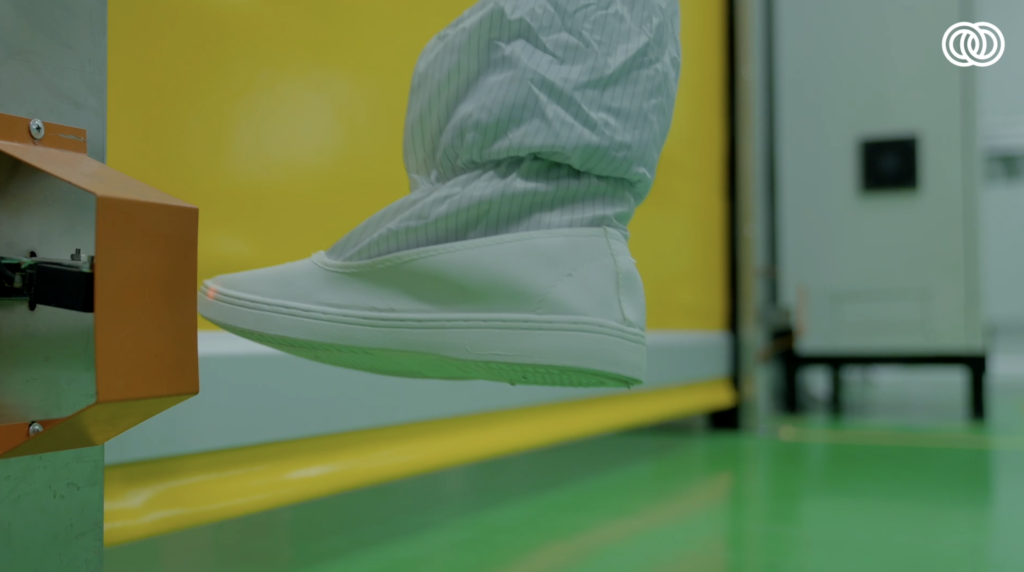
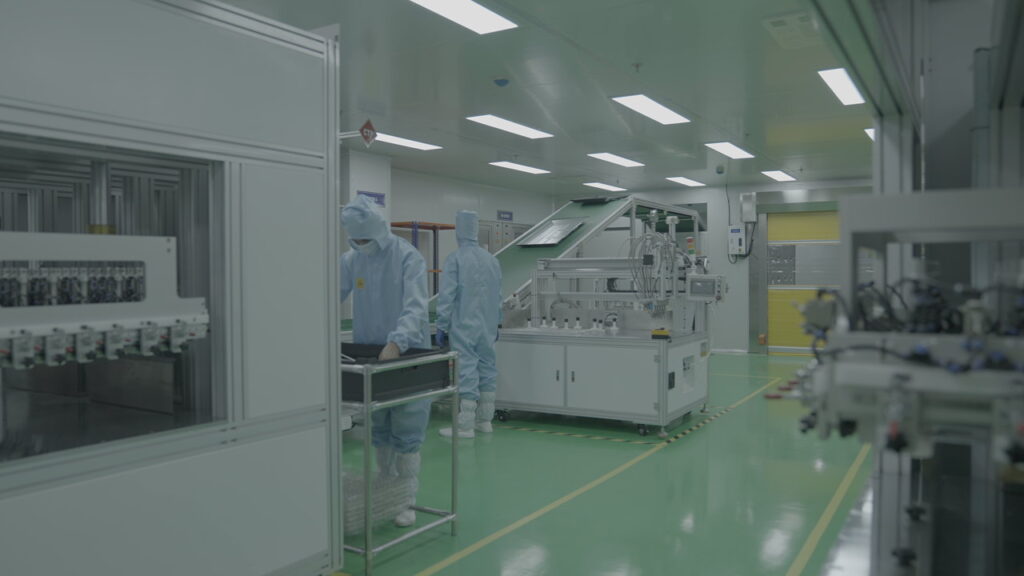
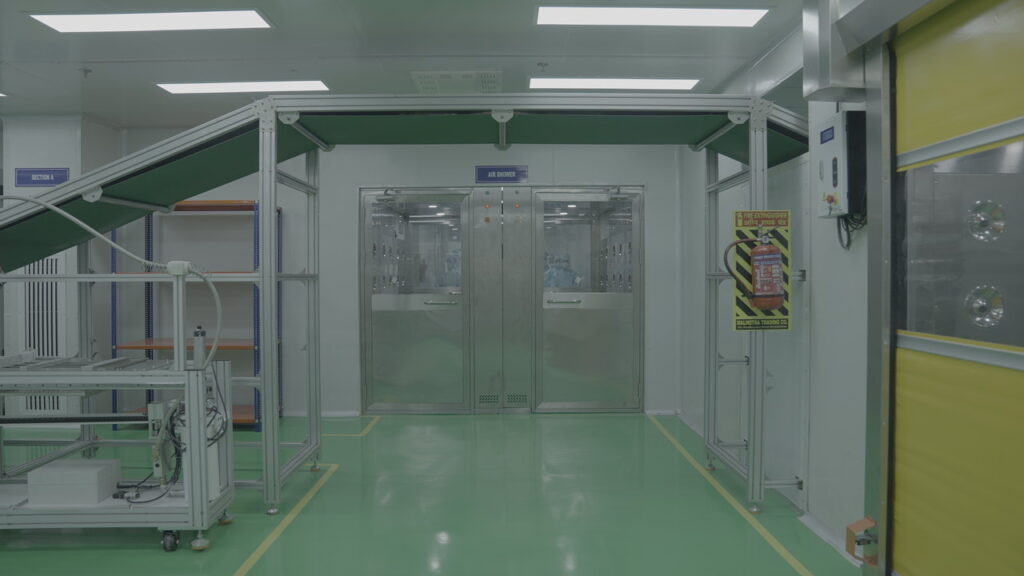
10k Clean Room LCM area
In a 10k clean room LCM area, the air is filtered and circulated through high-efficiency particulate air (HEPA) filters to remove contaminants. The temperature, humidity, and air pressure are also carefully controlled to maintain a consistent and stable manufacturing environment. Personnel working in the clean room typically wear specialised clothing and follow strict protocols to prevent contamination.
In-line ageing capabilities typically utilise specialised equipment and testing protocols that allow us to simulate the ageing process for our products.
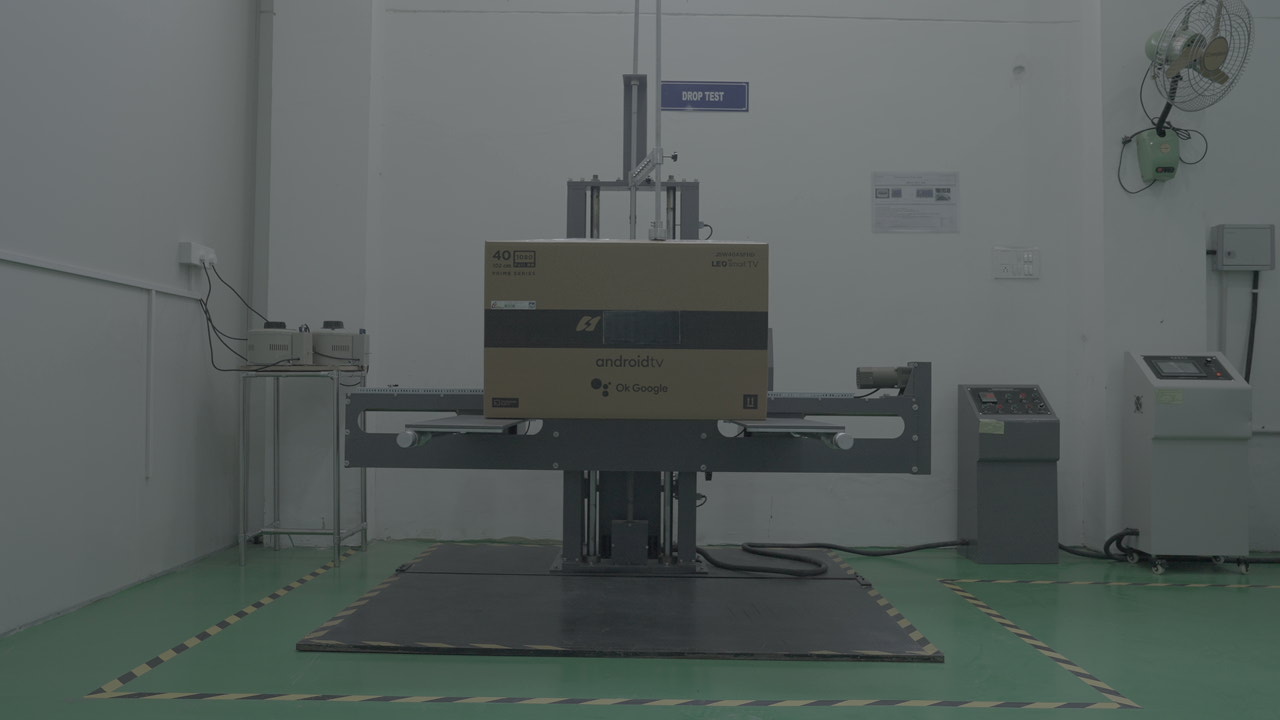
Inhouse Reliability:
Inhouse Reliability entails the utilisation of a dedicated test room equipped with facilities for conducting Drop tests, Vibration tests, and spike tests. Additionally, ELT rooms can perform comprehensive temperature and humidity checks across all device models.
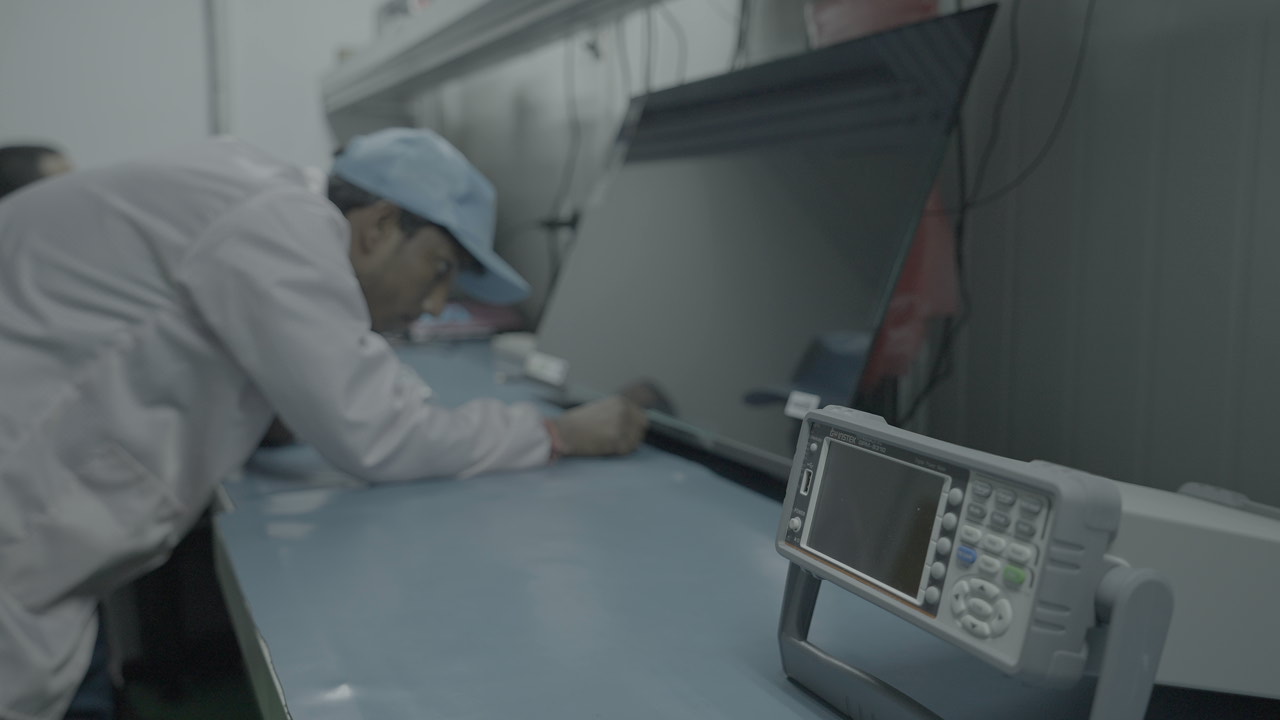
Automated Test Equipment (ATE):
Automated Test Equipment (ATE) is a sophisticated computer-controlled system for testing electronic devices, including smart devices. Its purpose is to execute a range of functional and reliability tests to ensure that the device conforms to the required standards.
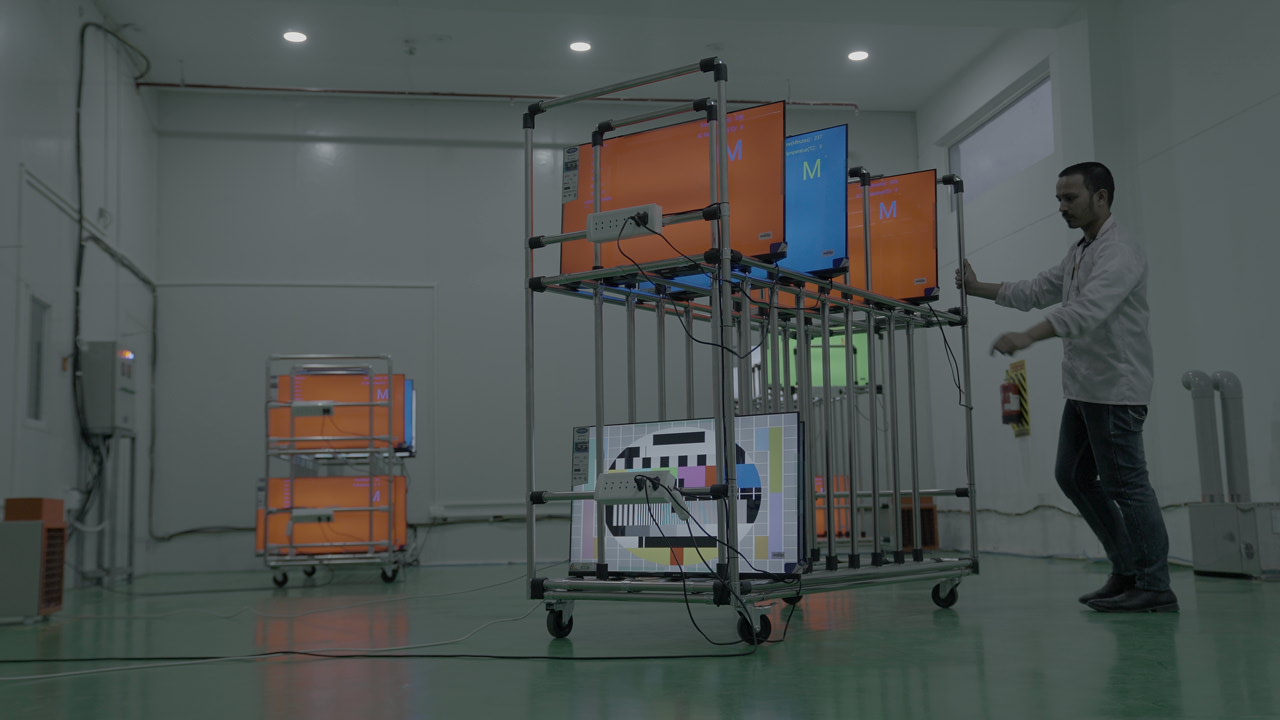
Environmental Testing:
Environmental Testing encompasses subjecting the device to various environmental conditions such as temperature, humidity, and vibration. The objective is to ascertain the device's capability to endure regular usage and potential mishandling.
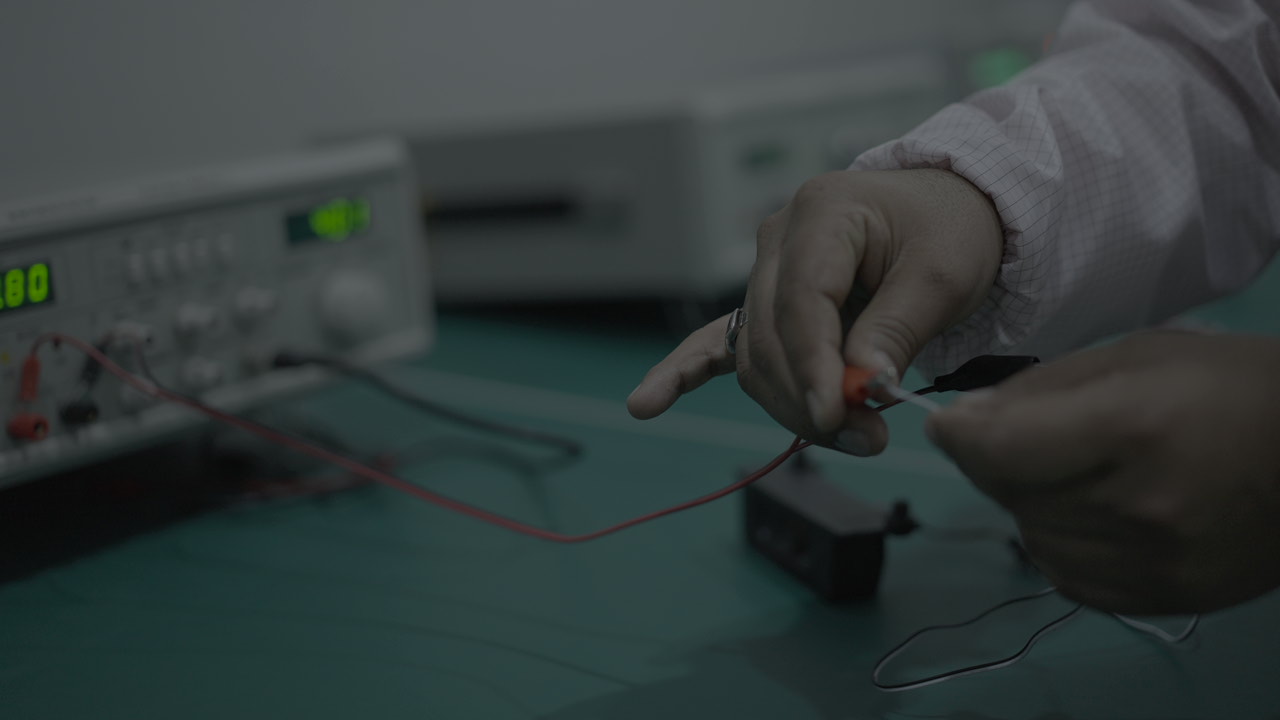
User Experience Testing:
User Experience Testing evaluates the device's usability and overall user experience. This encompasses comprehensive testing of the device's interface, navigation, and other user-facing features to ensure they are intuitive and user-friendly.
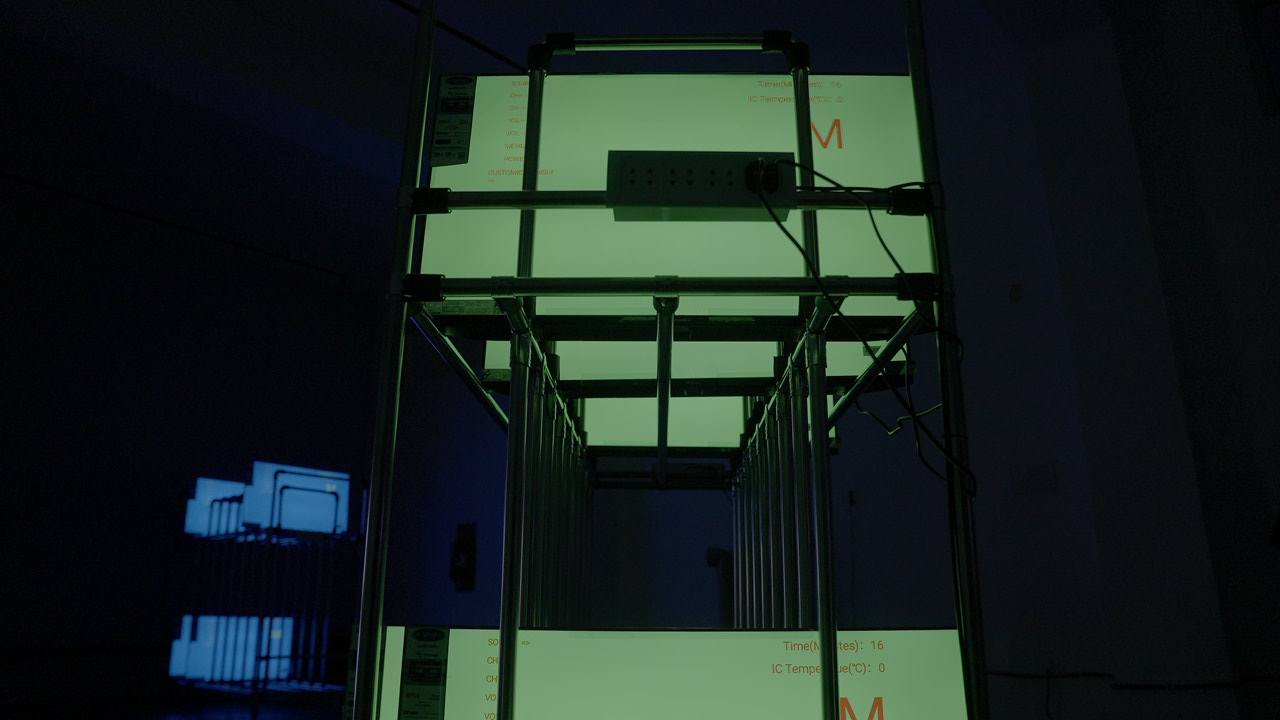
Compatibility Testing:
Compatibility Testing involves evaluating the device's compatibility with diverse software and hardware configurations. This rigorous testing guarantees the device functions correctly across different operating systems, applications, and other devices.
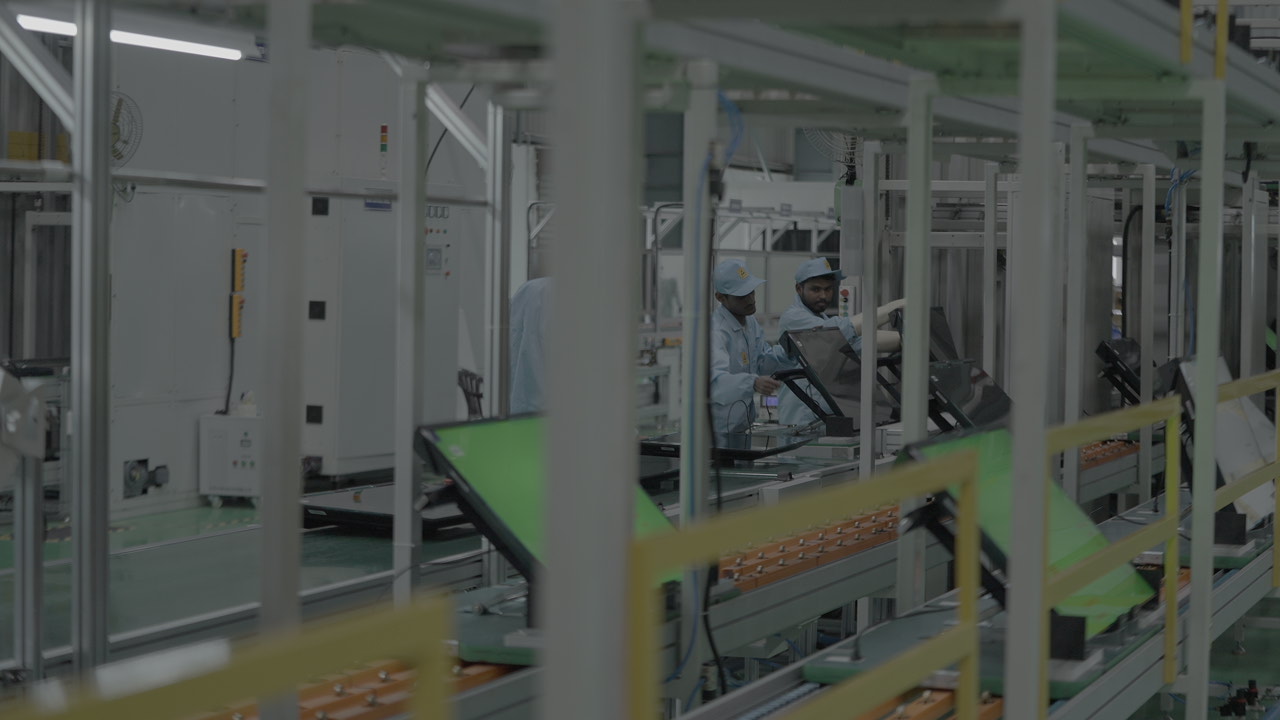
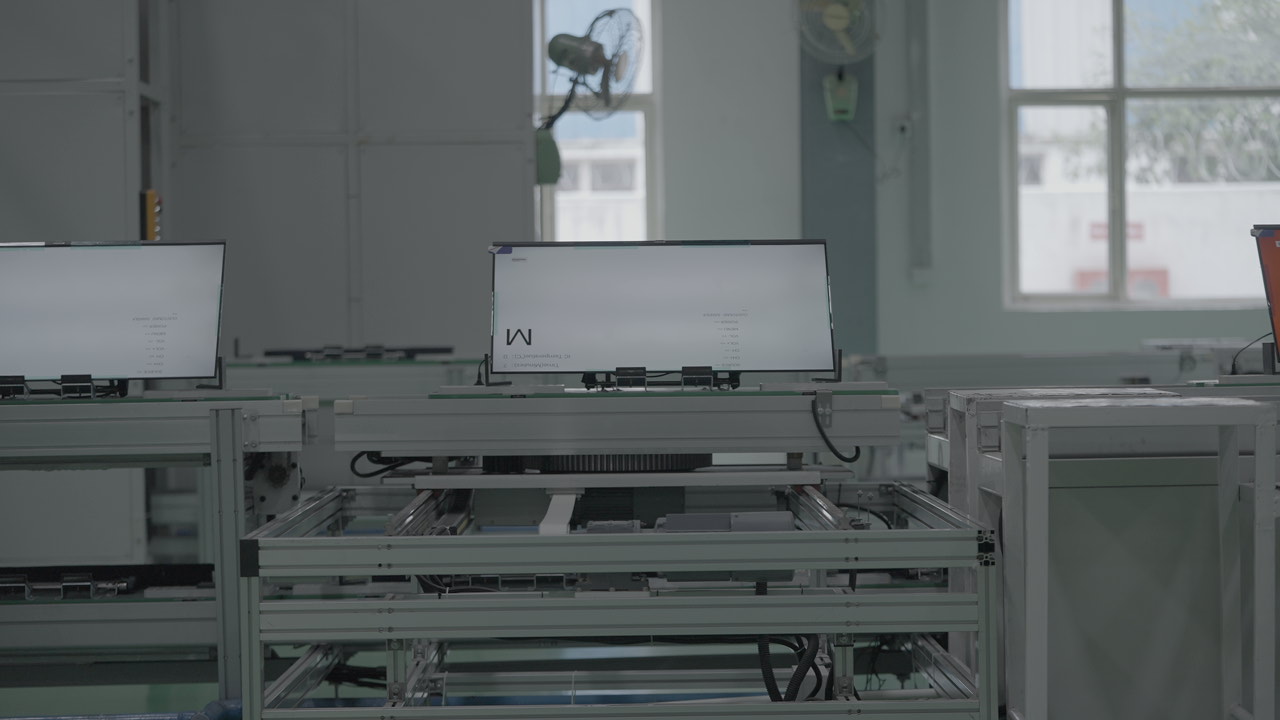
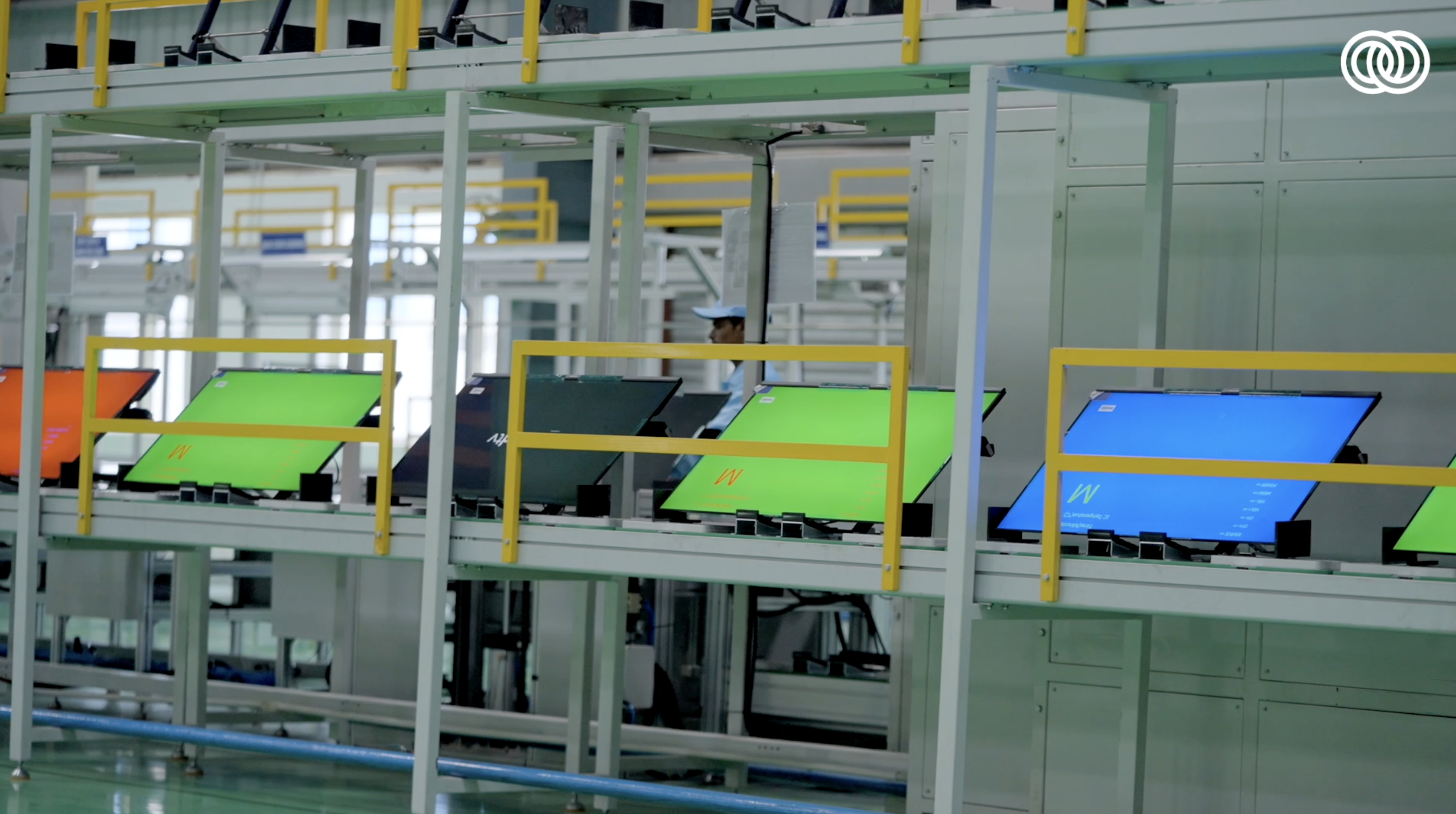
Managing In-line Ageing
Managing in-line ageing involves subjecting products to various conditions and stressors that simulate the normal wear and tear they may experience over time. As a part of this process, we conduct rigorous testing and analysis of long-term performance and durability during manufacturing, including exposure to heat, humidity, vibration, and other environmental factors. In-line ageing capabilities typically utilise specialised equipment and testing protocols that allow us to simulate the ageing process for our products.
In-line ageing capabilities typically utilise specialised equipment and testing protocols that allow us to simulate the ageing process for our products.
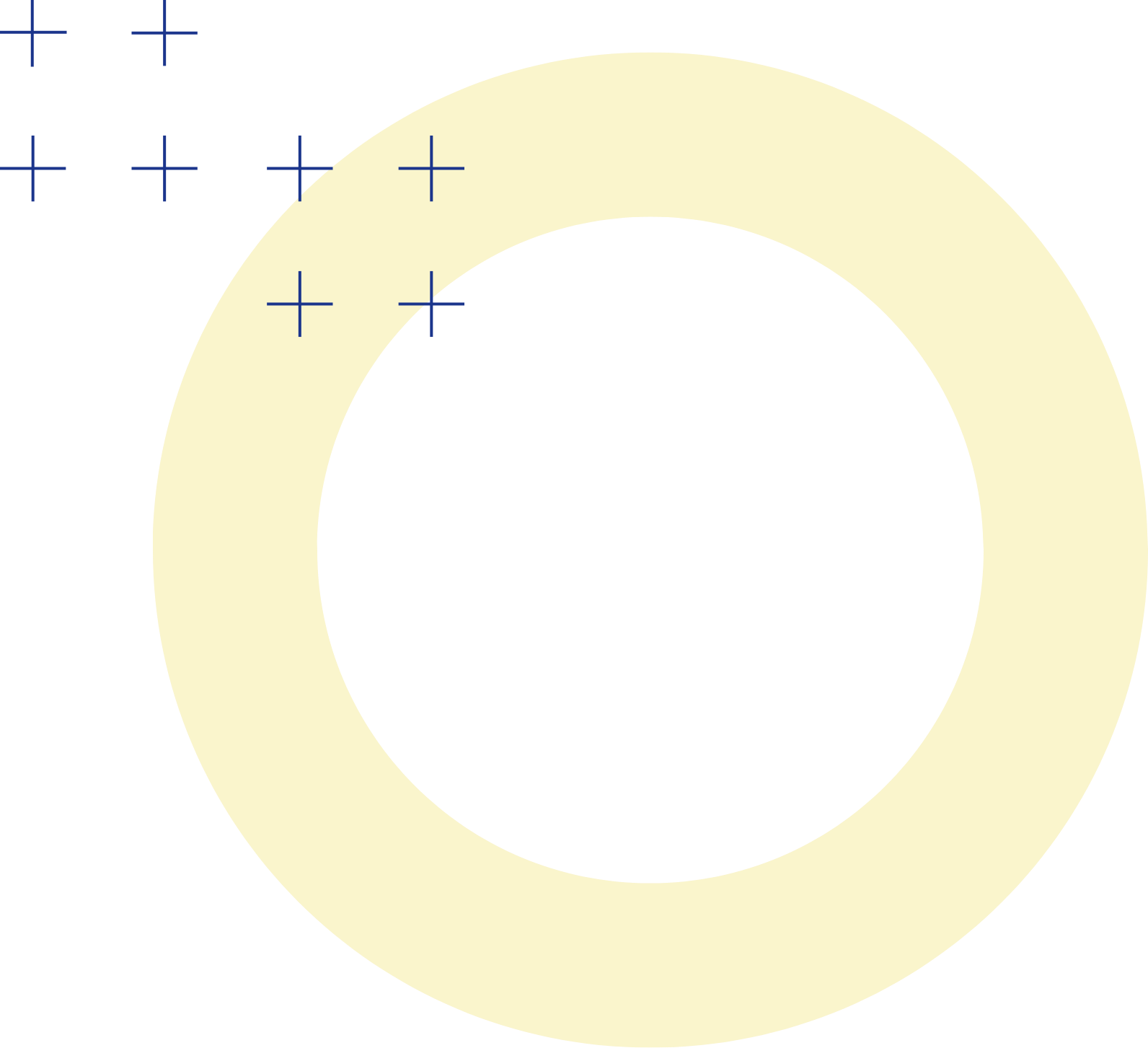
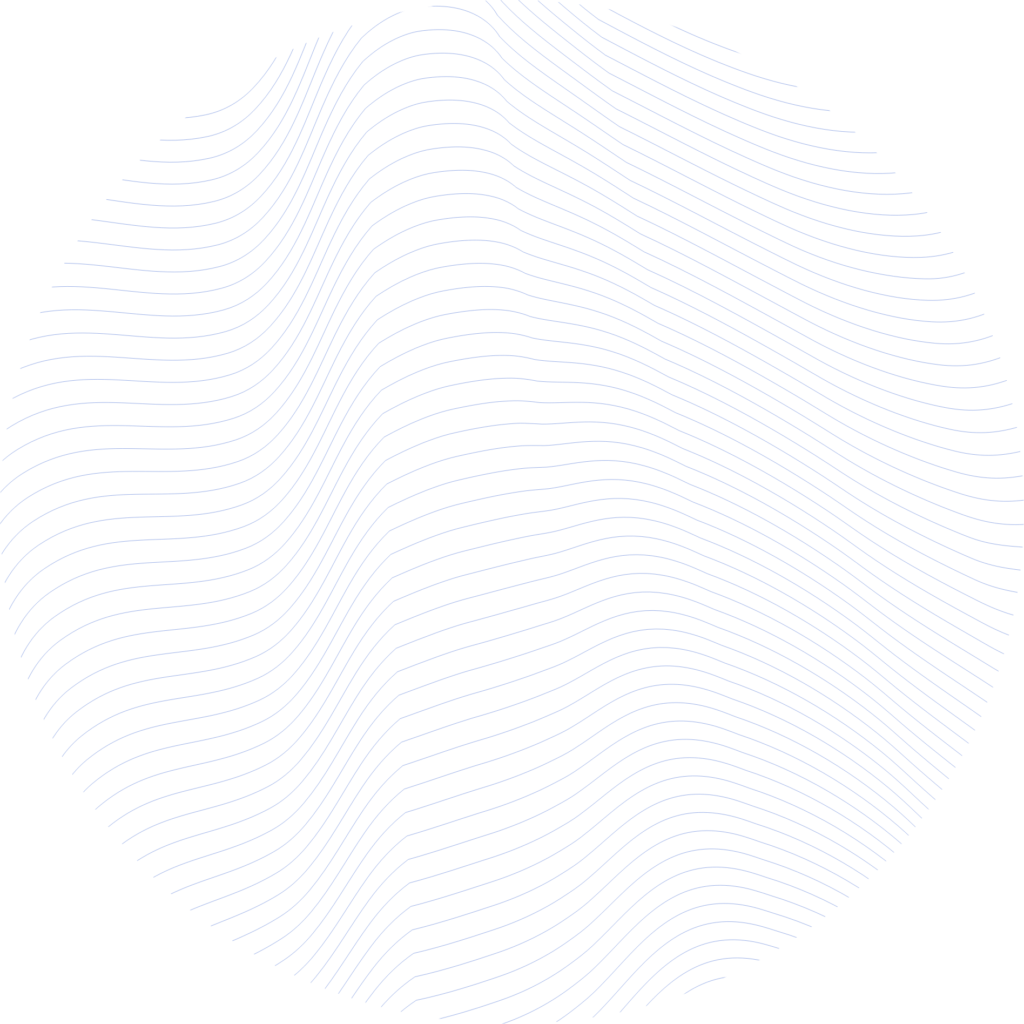
Warehousing
Managing raw materials and finished goods warehousing for consumer electronics entails several vital steps to ensure the safe and efficient storage of materials and products. The process may include the following:
- Receiving and Inspecting Materials
- Storing Materials
- Tracking Inventory
- Picking and Shipping Orders
- Quality Control
- Quality control involves inspections and testing of the materials and products at various process stages.
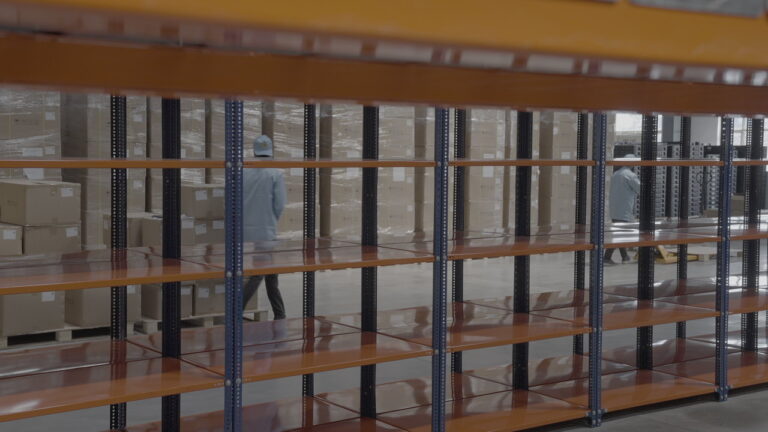
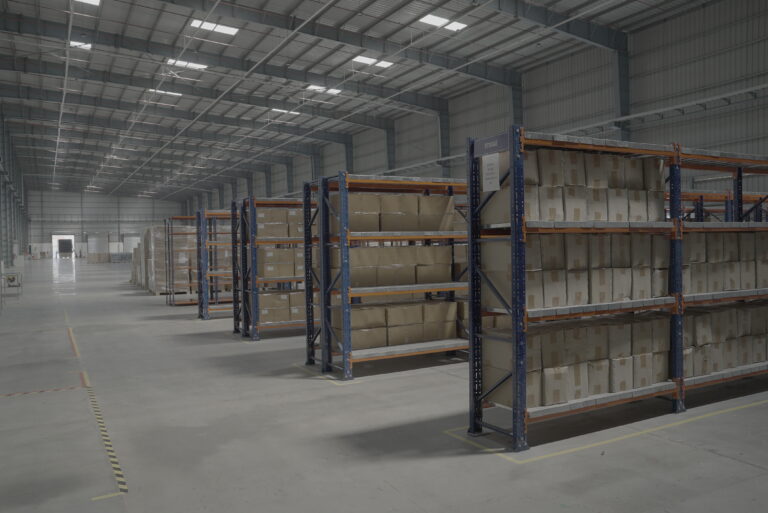
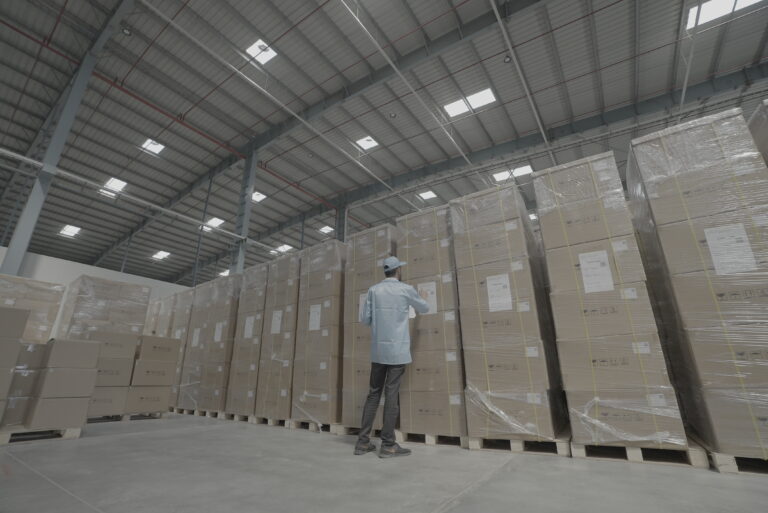
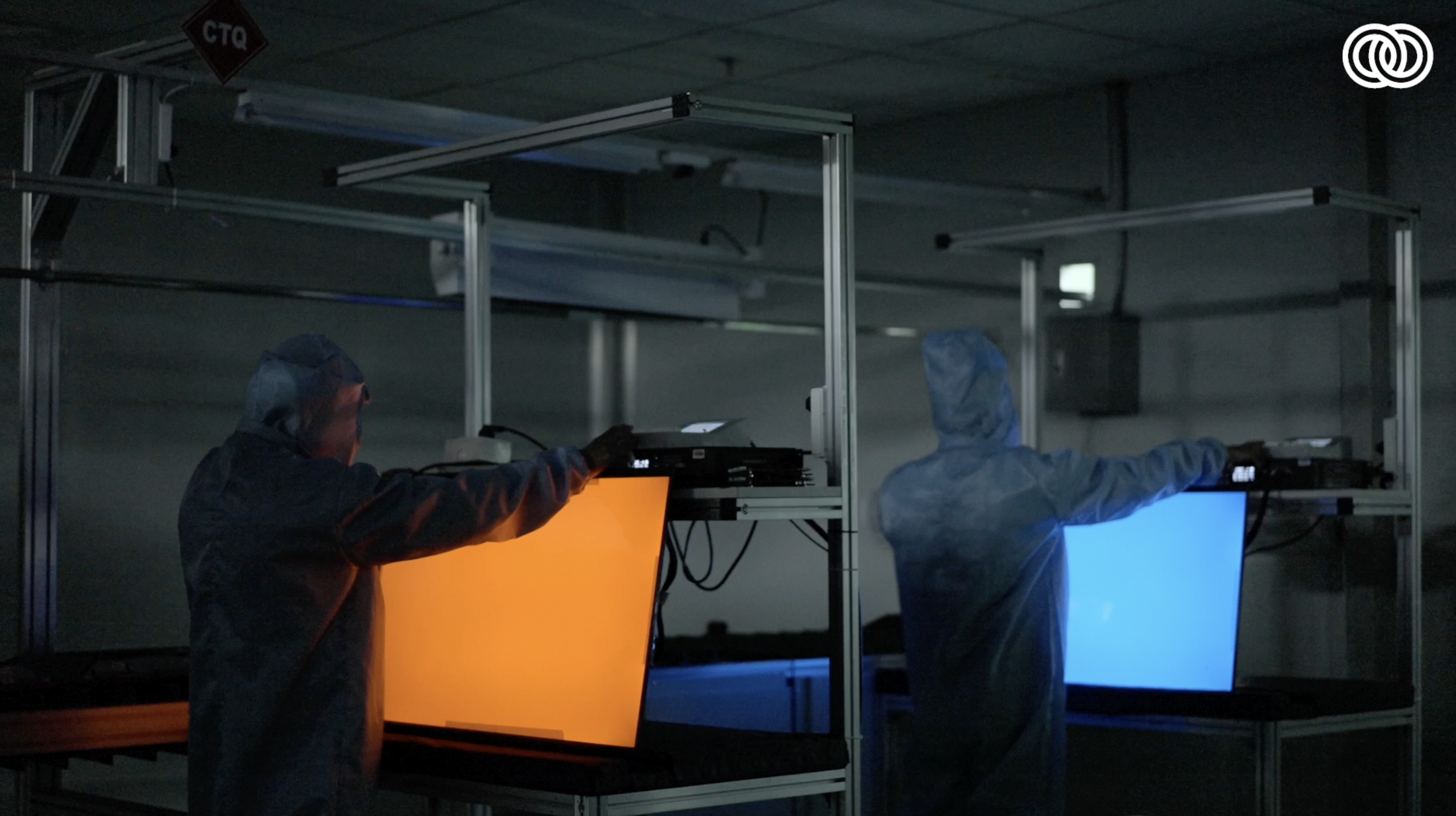
Repairs maintenance and after-sales capability
This comprehensive process identifies and fixes any product issues. The specific steps may vary depending on the product type and the extent of repairs needed but generally include the following: In-house maintenance team available 24×7 to address minor and major issues Utilisation of trained and advanced repair and maintenance equipment
In-line ageing capabilities typically utilise specialised equipment and testing protocols that allow us to simulate the ageing process for our products.
- Proper diagnosis of issues
- Efficient repair of the product
- Thorough testing to ensure functionality
- Ongoing maintenance support
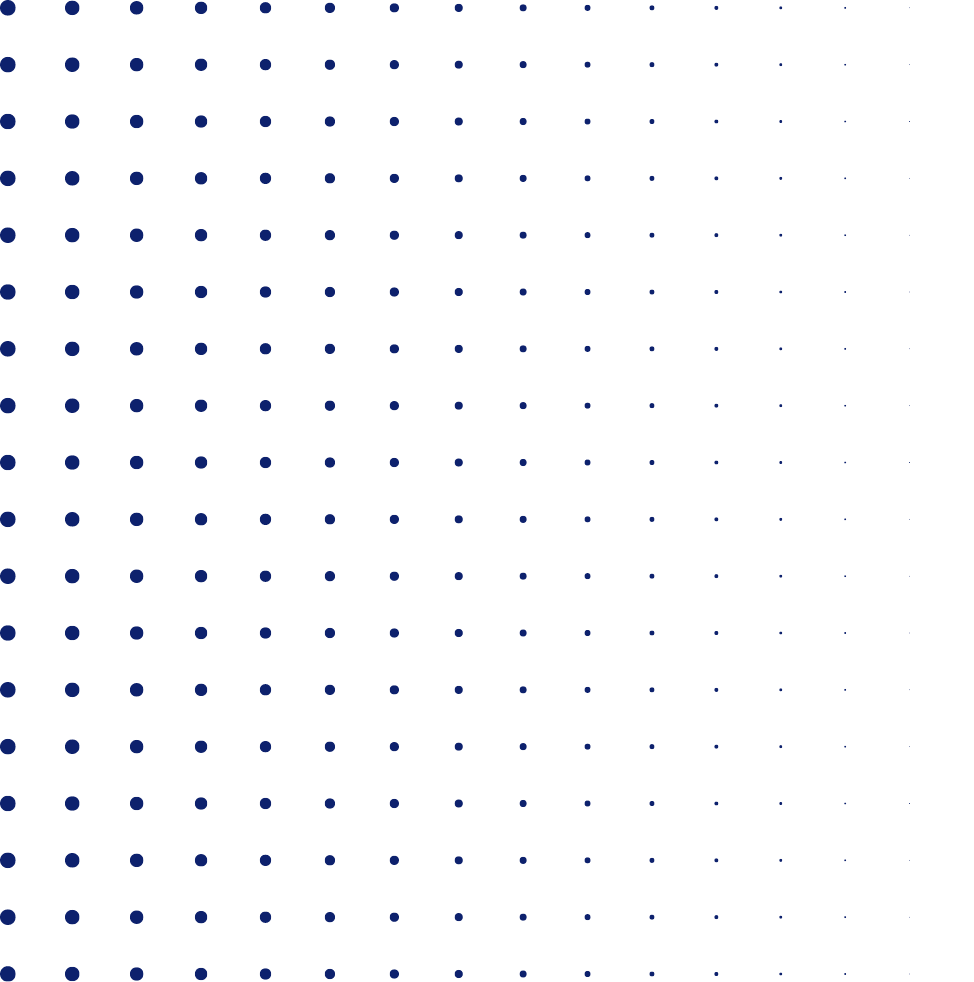